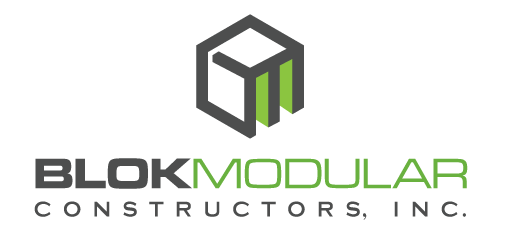
The Rise of Prefab Commercial Buildings:
A Revolution in Construction
The construction industry has witnessed a remarkable transformation over the years, with innovative technologies and methodologies paving the way for more efficient, cost-effective, and sustainable building practices. One such revolution in construction is the widespread adoption of prefab (prefabricated) commercial buildings. These structures, which are manufactured in a controlled environment and assembled on-site, have gained popularity for their ability to deliver high-quality, custom-designed, and energy-efficient commercial spaces. In this article, we will explore the world of prefab commercial buildings, shedding light on their benefits, the technology behind them, design flexibility, environmental advantages, and the future of this evolving construction trend.
The Prefab Commercial Building Process
Prefab commercial buildings, also known as modular buildings, are constructed using a systematic process that combines advanced manufacturing techniques and on-site assembly. This approach differs significantly from traditional construction methods, where buildings are constructed piece by piece on-site. The prefab process involves the following key stages:
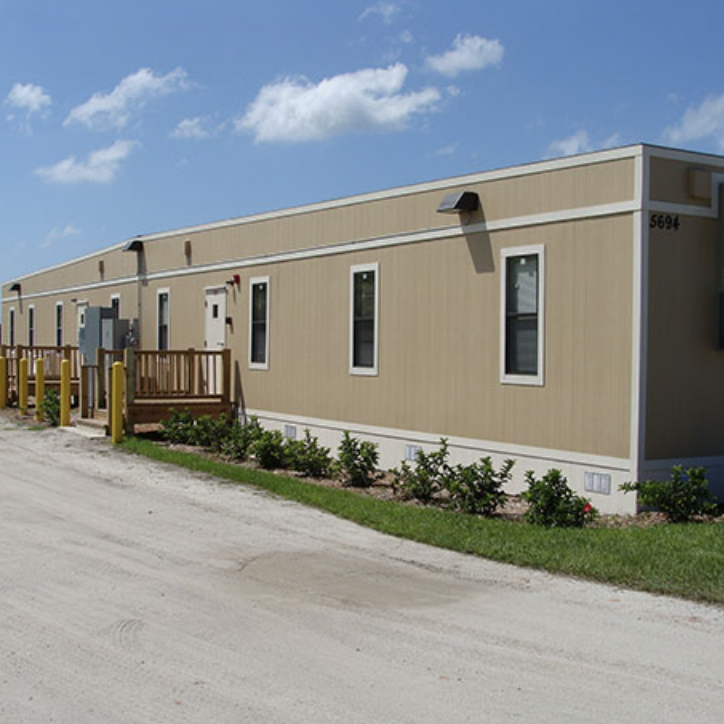
Design and Engineering: The journey of a prefab commercial building begins with the design phase. Architects and engineers work together to create detailed plans and specifications that outline every aspect of the structure. This process allows for customization, ensuring that the building meets the specific needs and requirements of the client.
Manufacturing: Once the design is finalized, the building components are manufactured in a controlled factory environment. This controlled setting ensures precision and quality control, minimizing the risk of weather-related delays and other on-site construction challenges.
Transportation: After the manufacturing process is complete, the building components are transported to the construction site. These components can range from wall panels, roofing elements, and even entire room modules, depending on the design and size of the building.
On-Site Assembly: The on-site assembly is typically faster than traditional construction. The components are fitted together like pieces of a puzzle, using cranes and specialized equipment. This phase requires skilled labor to ensure that the building comes together accurately and efficiently.
Finishing and Integration: Once the building is assembled, the finishing touches are added. This includes interior finishes, HVAC systems, electrical work, plumbing, and any other necessary integrations. The building is then ready for occupancy.
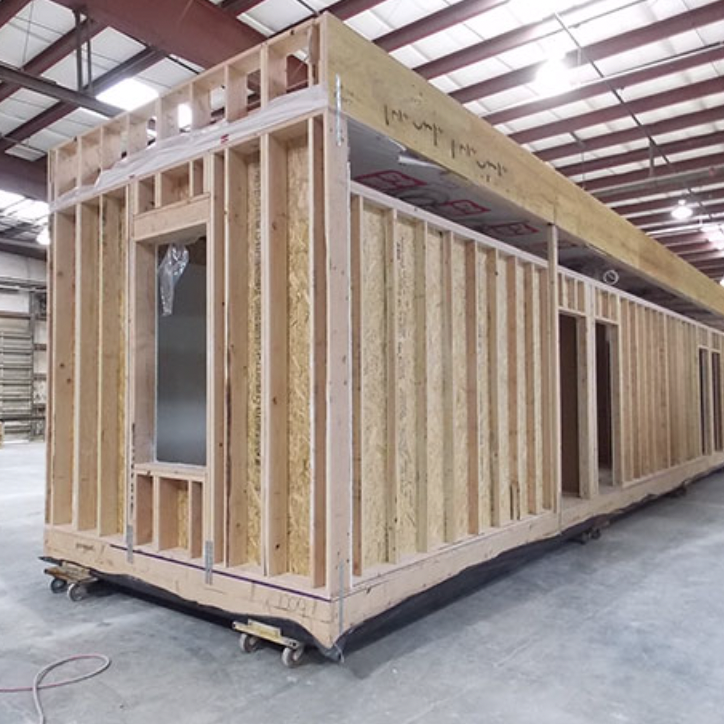
Benefits of Prefab Commercial Buildings
Speed of Construction: One of the primary advantages of prefab commercial buildings is the significantly reduced construction time. Traditional construction projects often face delays due to adverse weather conditions, but prefab buildings are manufactured indoors, reducing the impact of weather on the construction timeline.
Cost Efficiency: Prefabricated construction is often more cost-effective than traditional building methods. The controlled manufacturing environment leads to reduced waste, better material utilization, and efficient labor allocation, resulting in lower construction costs.
Design Flexibility: Prefab commercial buildings offer a high degree of design flexibility. They can be customized to meet the unique needs of businesses, allowing for a wide range of architectural styles and layouts. Whether it’s a retail space, an office building, a healthcare facility, or a school, prefab buildings can be tailored to suit the requirements of the client.
Sustainability: Sustainability is a significant driver for the adoption of prefab construction. The precision manufacturing process reduces material waste, and the ability to incorporate energy-efficient features and technologies makes prefab buildings environmentally friendly. In many cases, these buildings can also be disassembled and relocated, reducing the carbon footprint associated with construction.
Quality Control: The factory-controlled environment in which prefab buildings are manufactured allows for rigorous quality control. Each component is fabricated to exacting standards, ensuring consistency and structural integrity. This results in a high-quality end product.
Reduced Disruption: Prefab construction minimizes on-site disruption and noise, making it an ideal choice for projects in urban areas or near sensitive environments. This is especially important for commercial projects where business operations need to continue without significant interruption.
Shorter Payback Period: Due to the speed of construction and the efficiency of prefab methods, businesses can occupy their commercial space sooner, leading to a shorter payback period on their investment.
Technology Behind Prefab Commercial Buildings
The success of prefab commercial buildings relies on advanced technology and manufacturing processes. Key technological elements include:
Building Information Modeling (BIM): BIM is a crucial tool in the design and planning phase. It allows architects and engineers to create a detailed digital representation of the building, which aids in planning and ensures that all components fit together precisely during assembly.
Computer Numerical Control (CNC) Machines: CNC machines are used in the manufacturing process to precisely cut, shape, and prepare building components. They ensure high precision, consistency, and quality in the fabrication of parts.
Advanced Materials: The use of innovative materials, such as engineered wood products and high-performance insulation, enhances the structural integrity and energy efficiency of prefab buildings.
Automation: Modern factories employ automation for various tasks, including component assembly, quality control, and transportation within the facility. This results in increased efficiency and reduced labor costs.
Design Flexibility
Prefab commercial buildings are not limited to a specific architectural style or layout. In fact, they can be customized to an impressive degree, allowing for a wide range of design options. Some key elements of design flexibility in prefab commercial buildings include:
Architectural Styles: Prefab buildings can adopt a variety of architectural styles, from modern and minimalist designs to traditional and ornate facades. The exterior appearance can be customized to align with the brand image or aesthetics desired by the client.
Interior Layout: The interior layout is highly adaptable. Whether you need open-concept office spaces, retail showrooms, partitioned office suites, or specialized areas like laboratories or classrooms, prefab buildings can accommodate your requirements.
Sustainability Features: Prefab buildings can easily incorporate sustainable features, such as energy-efficient lighting, HVAC systems, and materials. Additionally, they can be designed to maximize natural lighting and ventilation, reducing energy consumption.
Expansion and Flexibility: Prefab buildings can be designed to allow for future expansion or reconfiguration. This adaptability ensures that the building can evolve with changing business needs.
Environmental Advantages
Prefab commercial buildings are making a significant contribution to sustainable construction practices. Some of the environmental advantages of these structures include:
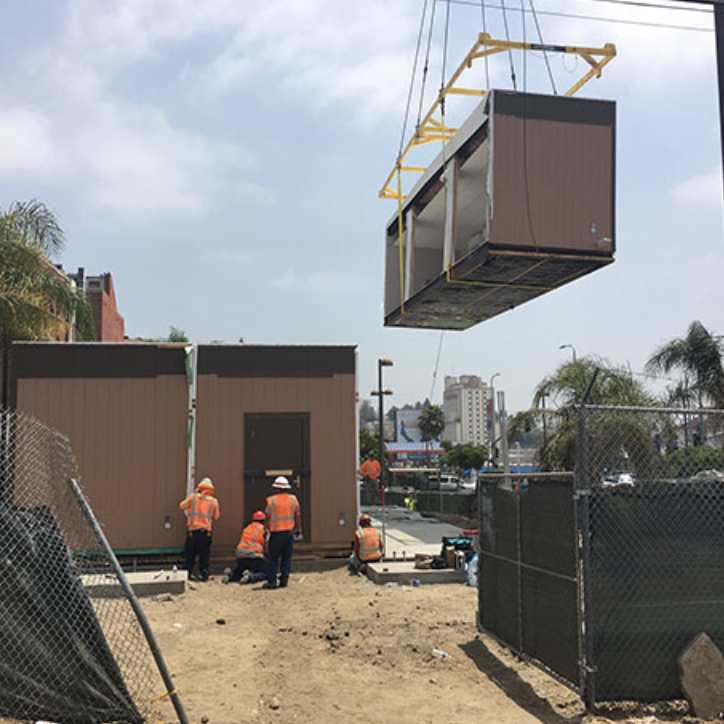
Reduced Waste: The controlled manufacturing environment of prefab buildings results in reduced waste compared to traditional construction. Precise measurements and material optimization lead to a more efficient use of resources.
Energy Efficiency: Prefabricated buildings can be designed with energy-efficient features, such as advanced insulation, efficient HVAC systems, and high-performance windows. These elements reduce energy consumption and operating costs.
Lower Carbon Footprint: The reduced construction time and the potential for building relocation contribute to a lower carbon footprint. Prefab buildings are not only built faster but also designed to be disassembled and reused, reducing the environmental impact of demolition.
Sustainable Materials: Many prefab buildings incorporate sustainable materials like engineered wood products, which are sourced from well-managed forests and promote responsible forestry practices.
Indoor Air Quality: Prefab buildings often feature advanced ventilation systems that enhance indoor air quality, creating a healthier and more comfortable environment for occupants.
The rise of prefab commercial buildings represents a significant shift in the construction industry, offering a range of benefits that cater to the needs of businesses, developers, and the environment. These structures not only provide cost-effective and efficient solutions but also offer design flexibility, sustainability, and high-quality construction. The technology behind prefab buildings, including BIM, CNC machines, and advanced materials, has played a crucial role in their success